

As maintenance planners spend most of their time in the maintenance system to plan work orders (e.g. Second, while you may be able to make this approach work from a technical perspective, it is still impractical from a user experience perspective.
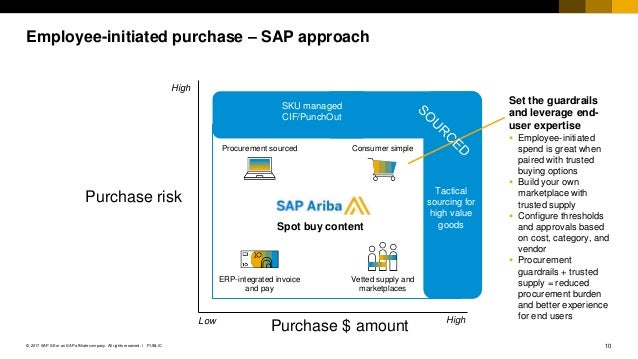
This usually isn’t practical because of high work order volumes, turnover and lack of additional descriptive data on the work order.
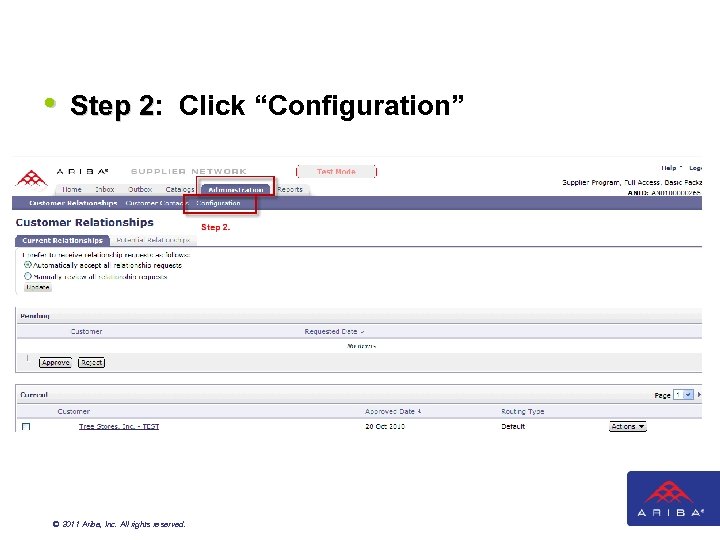
This is necessary so users can select these orders as account assignment objects to assign the costs of their purchase to the work order. This poses a few problems for maintenance purchases as they usually need to be tied to a work order to track maintenance costs.įirst, to associate a purchase to a work order with the above use case, you would need to import all active work order numbers into your S2P tool. The requisition is then submitted for approval to initiate the rest of the process (PO, GR, Invoice). From there, users search materials and/or services to build their requisitions. The typical process usually starts in the S2P application with a requisition and/or shopping cart. However, the general concepts could apply to any catalog management platform / back end combination.

I’ve used SAP Ariba Catalogs with an SAP Materials Management / Plant Maintenance back end system in the article examples. Furthermore, I touch on the benefits associated to such an endeavor and how to go about building your business case. The following article details how you would use a catalog management platform (CMP) to achieve this in the maintenance context. By using maintenance catalogs, you can drive efficiency in your maintenance planning process and get through your maintenance backlog. Thankfully, you can drive benefits in the maintenance department by leveraging the catalog management modules of S2P technologies. This is true of all leading Source to Pay (S2P) suites (SAP Ariba, Ivalua, Coupa, Jaggaer, Zycus, etc.). M aintenance teams are underserved by the standard indirect purchasing Source to Pay (S2P) technology use case.
